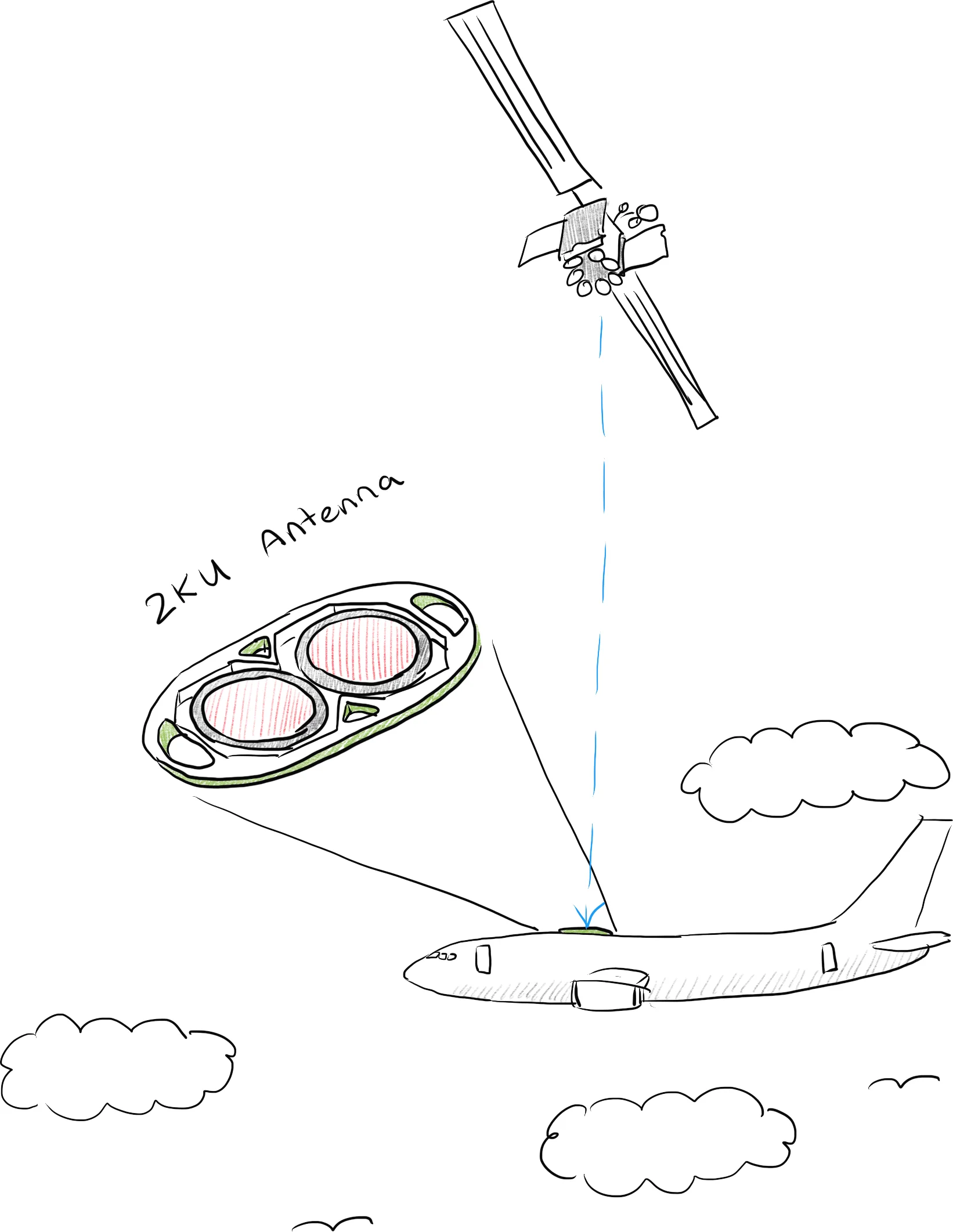
Aircraft Radome Install System
This system design began as an all machined design, leveraging an extruded aluminum spine and cross beam. To reduce the cost of production, milled aluminum was switched to 3D printed nylon, drastically improving weight and lead time. This project was challenging in numerous ways. To start, multiple parties were involved—four different companies to be specific. The engineering design and development had to be carefully managed, tracked, and communicated to avoid confusion. The schedule was strenuous. We were typically given 3 weeks between iterations to come up with the designs, implement them, document it and deliver physical parts. Adding to the challenge, this was also the first design and manufacturing project for the engineering service company I worked for. This meant that as the design was created and developed, all revision control, engineering change orders, part number systems, manufacturing contacts, quality systems etc. had to be established for the first time and used immediately. Luckily I could draw from my medical device design and documentation experience to establish these systems. Additionally, I was the only engineer working on the project while also wearing the hats of people manager and project manager. These factors combined to yield a very, very difficult project. But this was my first foray into aerospace, and I gave it my full effort. By the time the final iteration of the prototype was delivered and tested, the client company granted us new contracts to design and develop installation tools for more aircraft.
Below you can see the progression of the design, as well as the tool field testing.
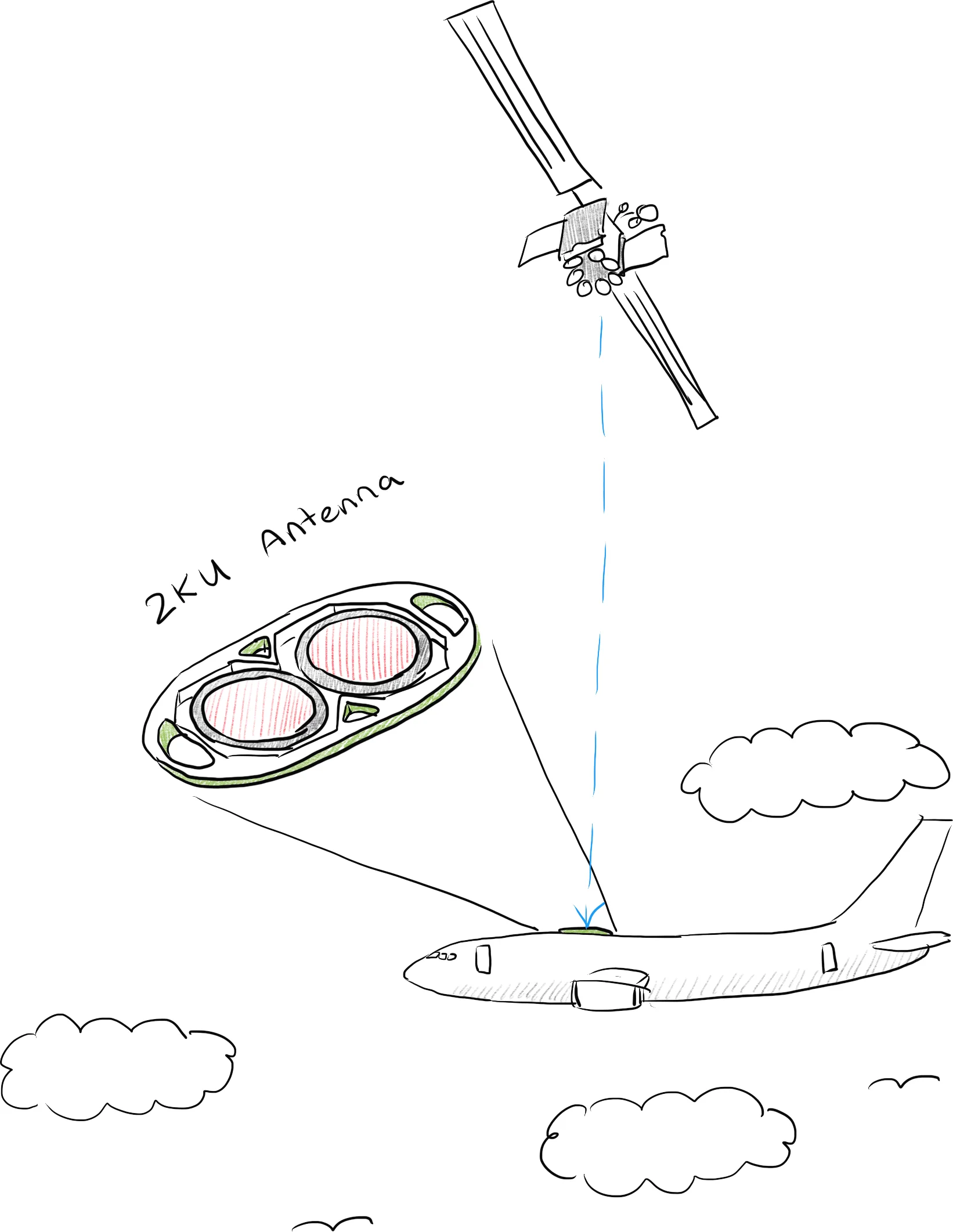
This system design began as an all machined design, leveraging an extruded aluminum spine and cross beam. To reduce the cost of production, milled aluminum was switched to 3D printed nylon, drastically improving weight and lead time. This project was challenging in numerous ways. To start, multiple parties were involved—four different companies to be specific. The engineering design and development had to be carefully managed, tracked, and communicated to avoid confusion. The schedule was strenuous. We were typically given 3 weeks between iterations to come up with the designs, implement them, document it and deliver physical parts. Adding to the challenge, this was also the first design and manufacturing project for the engineering service company I worked for. This meant that as the design was created and developed, all revision control, engineering change orders, part number systems, manufacturing contacts, quality systems etc. had to be established for the first time and used immediately. Luckily I could draw from my medical device design and documentation experience to establish these systems. Additionally, I was the only engineer working on the project while also wearing the hats of people manager and project manager. These factors combined to yield a very, very difficult project. But this was my first foray into aerospace, and I gave it my full effort. By the time the final iteration of the prototype was delivered and tested, the client company granted us new contracts to design and develop installation tools for more aircraft.
Below you can see the progression of the design, as well as the tool field testing.

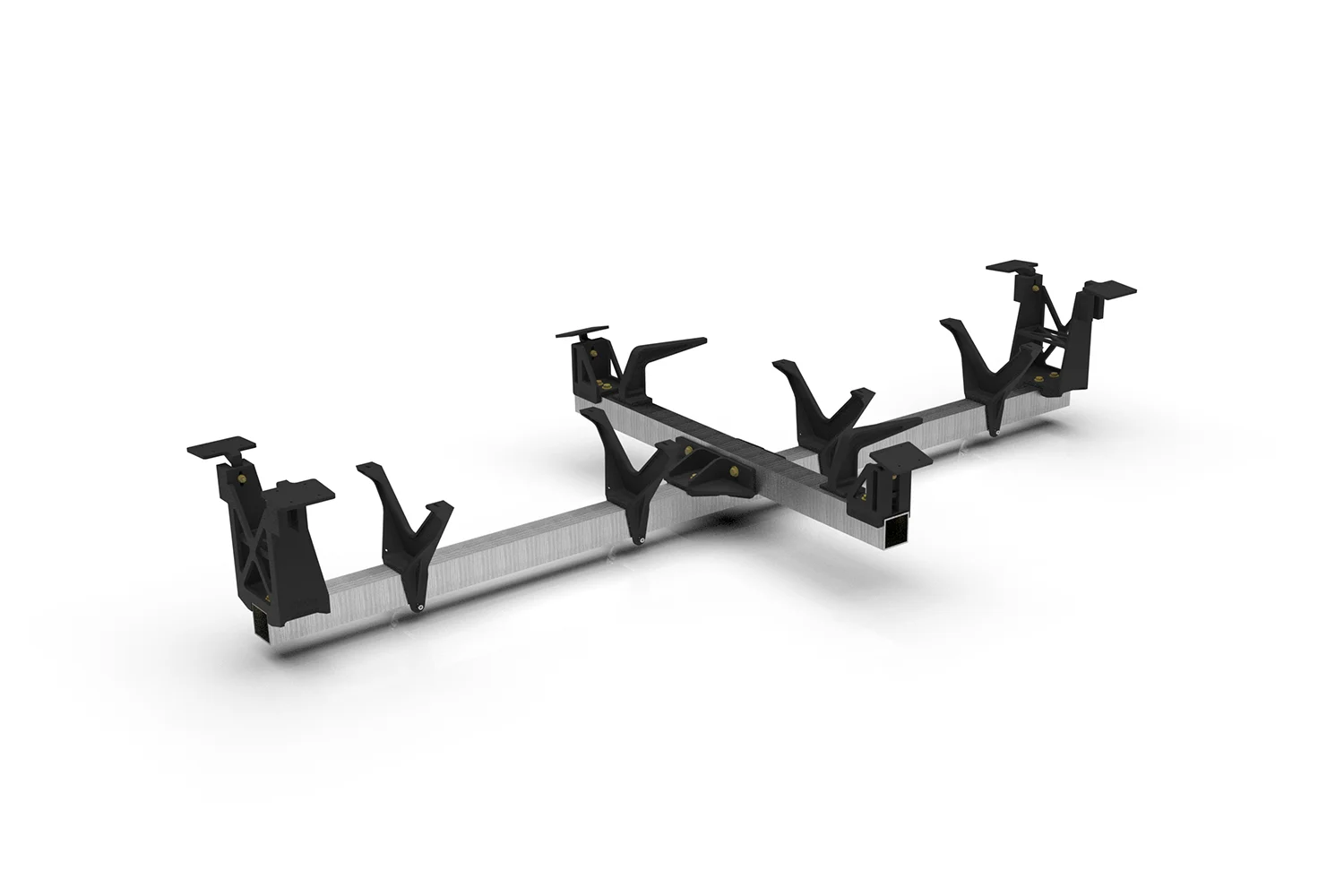

